精密部品製作
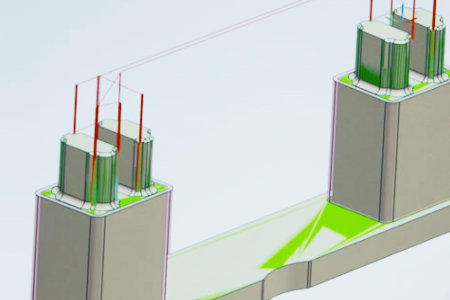
CAD
Step1:データ作成
お客様より頂いた、図面、2次元データ、3次元データより当社の加工データに変換致します。図面不具合、矛盾などのチェックも含めた確認をおこない、弊社CAD/CAM技術は好評をいただいております。
※受取可能なデータ
2次元データ(.dxf/.dwg/.plsなど)
3次元データ(.prt/パラソリッド各種/.stl/.iges/.step/.proe/CATIAなど)
この他殆どのデータ受取が可能です。
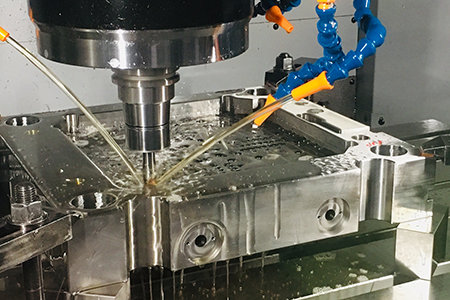
高速マシニング
Step2:製作工程
各工程にNCデータが送信されて、加工スタート致します。
熱処理を含め全てが社内製作のため、短納期での製作が可能です。
※各種メッキ処理などは外部委託
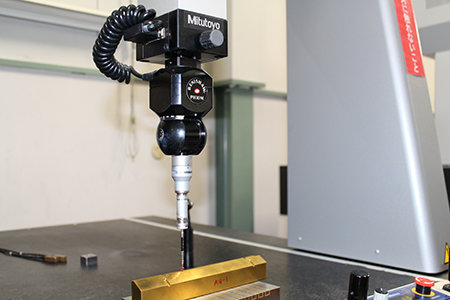
品質管理
Step3:製品測定
完成した商品の測定で不具合があれば、修正などの対策を施します。
※各工程での当社精度保証体制のため、この時点での不具合は
殆どありません。
Step4:出荷
当社で品質保証された商品がお客様に発送されます。
金型製作の生産工程
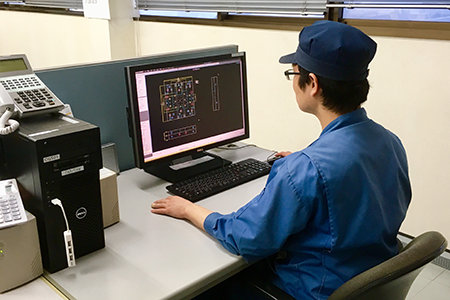
設計
Step1:金型設計
経験豊富な当社の設計スタッフが、製品図面にて綿密な仕様打合せを行い、
お客様の満足のいく金型設計を行います。
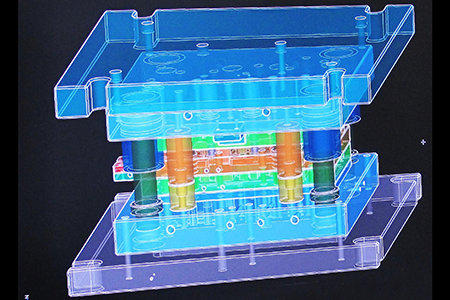
3D金型モデル
Step2:組図完成
金型組図が完成すると検図に入ります。
この時点でハイレベルの金型図面完成です。
Step3:データ作成
2、3次元で設計された金型図から、CAMオペレーターが工程毎の高精度データを社内LANで高速送信いたします。
マシニング加工から電極データまで加工理論の技術を持ったスタッフが担当しております。
Step4:製作工程
当社は金型製作をする上において一番重要な熱処理については、安定した最高の熱処理を追及するために材料メーカーと
熱処理条件を調整しつつ、社内に5基の真空熱処理を有してサブゼロ処理も含めて高品位の材料に仕上げています。そして新規の材料については、テストピースで
経年変化の調査も徹底しておこないます。
このように社内で材料特性を100%引き出してこそ、超精密加工の領域の平面研削加工、放電加工などの製作工程で図面規格をクリアした
高精度の金型部品が生産されてくるわけです。金型製作のプロは、熱処理でもプロでなければならないのです。
真空炉
平面研削
放電
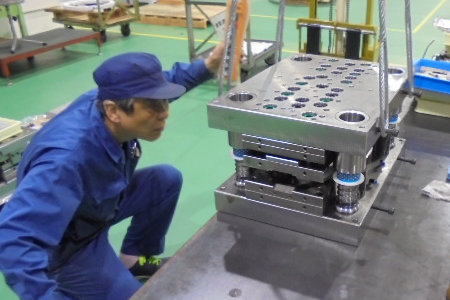
DAI組立て
Step5:金型組立て
熟練金型仕上げ担当者が寸分の狂いも無く、見事なまでに精密金型を組み上げていきます。そして、妥協を許さない職人気質で納得いくまで微調整をいたします。
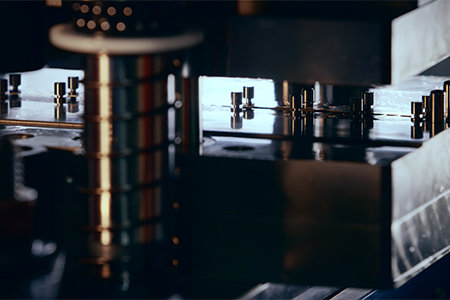
金型
Step6:トライ(仕打ち)
完成した金型のトライを行います。
(打ち抜き金型はプレス機/プラスチック金型は成形機)
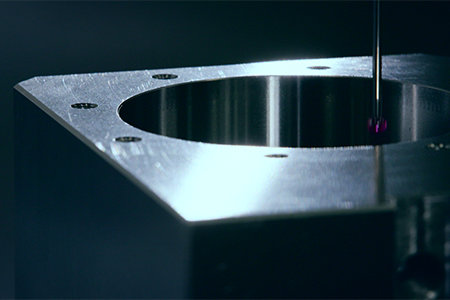
測定
Step7:製品測定
トライをしたサンプルの検定(測定)を高精度測定器で行います。
数ミクロンの公差外れでも再調整をして、納得のいく状態で出荷いたします。
そして、お客様に検定データの合否連絡をいたします。
Step8:金型出荷
完成した金型は、一刻も早くお客様に発送致します。
加工技術
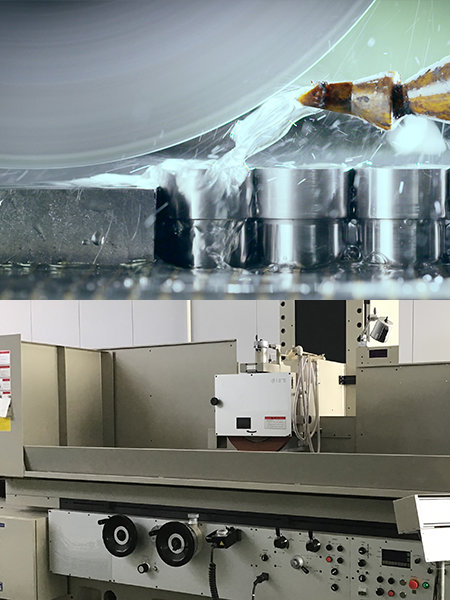
平面研削
- 面粗度
- 0.15S
- ピッチ精度
- ±1μ
- 砥石成形幅
- 0.09
- 最小コーナーR
- 0.02R
- 最大ワークサイズ
- 2,000×850
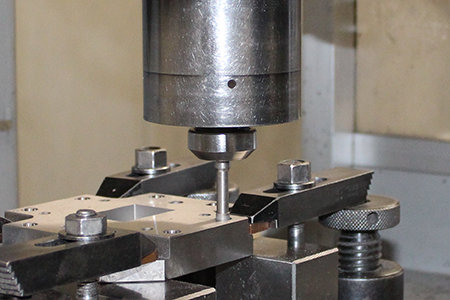
冶具研削技術
- φ0.15の内面研削
- 公差±1μ
- 異形状のチョッピング加工精度
- 公差±2μ
- 500ミリでのピッチ精度
- 公差±2μ
- φ200においての真円度
- 1.5μ
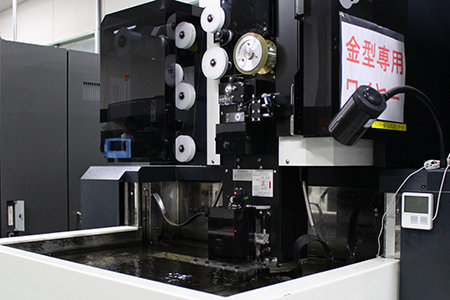
ワイヤー加工技術
- φ0.02ワイヤー線加工(微細ギヤー加工)
- 面粗度(油加工)
- 0.8S
- 面粗度(水加工)
- 1.5S
- 板厚=200タイコ量
- 0.0024
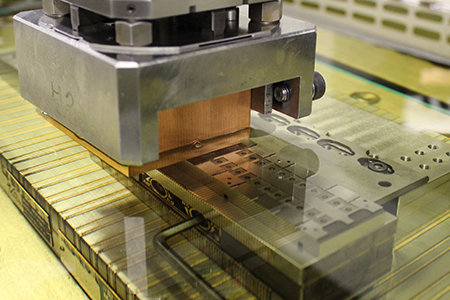
放電加工
- 面粗度
- 0.6S
- 最小コーナーR
- 0.017R
- 微細穴加工径
- φ0.05
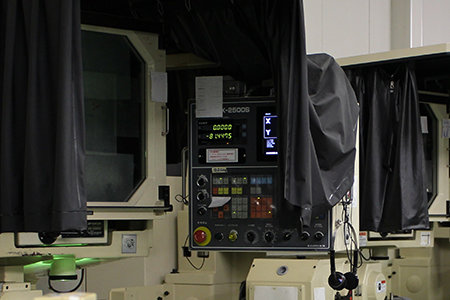
プロファイル
- 最小コーナーR
- 0.015R
- 面粗度
- 0.2〜0.3S
- 形状精度
- ±1.5μ
(微細ギヤーの形状精度)
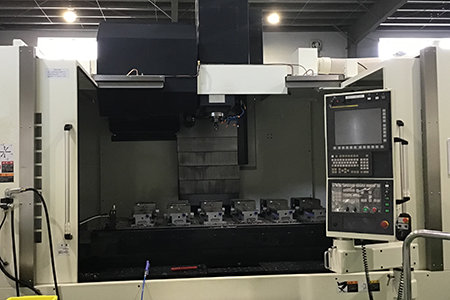
マシニング
- ワークサイズ
- 2,060×940
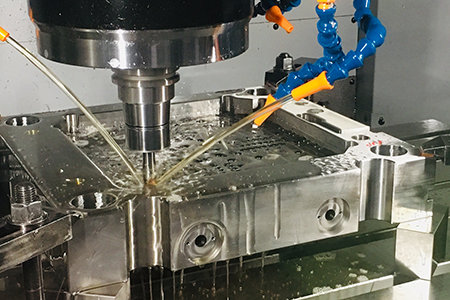
高速マシニング
- 工具交換時段差
- 2μ
- 使用最小径工具
- φ0.1
- 加工可能硬度
- HRC65